液冷系统的成本结构受应用场景、技术路线(如冷板式、浸没式)、材料选择和规模化程度影响显著。以下从部件成本、技术变量和场景差异三个维度展开详细分析:
一、典型液冷系统部件成本占比(以服务器液冷为例)

注:
- 消费电子(如笔记本)
冷板+工质占比可超60%,因空间限制需高精度加工; - 数据中心
冷板+泵+散热器合计占50%-70%,且需冗余设计增加成本; - 工业设备
管路系统占比提升(耐腐蚀要求高),可能超过20%。
二、技术路线对成本的影响
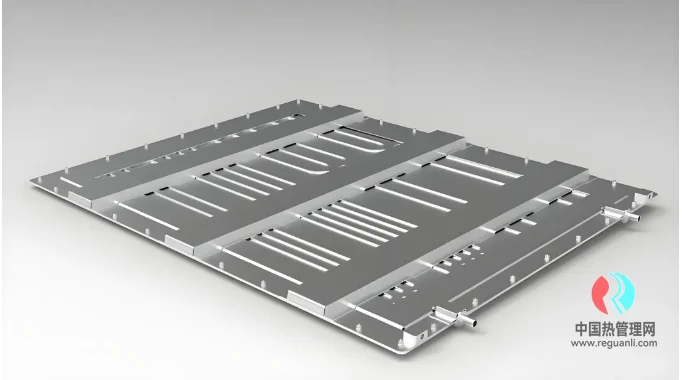
1.冷板式 vs 浸没式
-
- 冷板式
硬件成本高(精密加工+密封),但维护成本低(模块化替换);
案例:英伟达DGX H100液冷方案中冷板成本占系统40%。 - 浸没式
工质成本占比激增(电子级氟化液单价>50/L) , 但可省去冷板。 案例:Meta浸没式液冷服务器单机架工质成本超2000。
- 冷板式
2.材料升级成本差异

-
- 铜冷板
成本约$50-100/块(取决于厚度与加工精度); - 铝冷板
成本降低40%-60%,但热导率仅为铜的1/3; - 石墨烯增强材料
成本是纯铜的2-3倍,但可减少30%体积。
- 铜冷板
-
-
基础版:仅温控+流量调节,控制单元成本<$50; -
AI优化版:集成机器学习芯片,成本升至$200-500。
-
三、规模化生产与成本下降曲线

典型案例:
-
华为FusionServer液冷方案:量产规模从10万台增至100万台后,单台成本下降52%; -
Tesla Dojo超算液冷系统:通过自研冷板+批量采购氟化液,成本较初代降低65%。
四、成本敏感度排序(以典型服务器液冷为例)
- 最高敏感部件
冷板(材料与工艺)>工质(类型与纯度)>泵(流量性能); - 可优化方向
-
替换铜冷板为铝基复合材料(降本30%但牺牲5%散热效率); -
采用矿物油替代氟化液(降本70%但需加强绝缘防护); -
通用型泵替代定制泵(降本40%但牺牲场景适配性)。
-
五、未来成本趋势预测(2023-2030)
- 技术突破
微通道冷板3D打印技术成熟后,成本有望再降25%; - 材料革命
碳纳米管增强液冷工质或使导热系数提升200%,但初期成本仍高; - 市场预测
2030年全球液冷市场规模将达$350亿,单位成本较2023年下降58%(年均降幅8.5%)。
六、低成本方案参考
- 入门级方案
铝冷板+齿轮泵+矿物油,适用于低功率场景(<5kW),成本<$100/节点; - 平衡方案
铜冷板+陶瓷泵+乙二醇基工质,适用于中功率(5-20kW),成本$200-500/节点; - 高端方案
浸没式+石墨烯冷板+氟化液,适用于超算/HPC,成本$1000+/节点。
通过精准匹配场景需求与技术规格,结合规模化采购和工艺优化,液冷系统成本可有效控制在目标区间内,同时满足散热效率与可靠性要求。